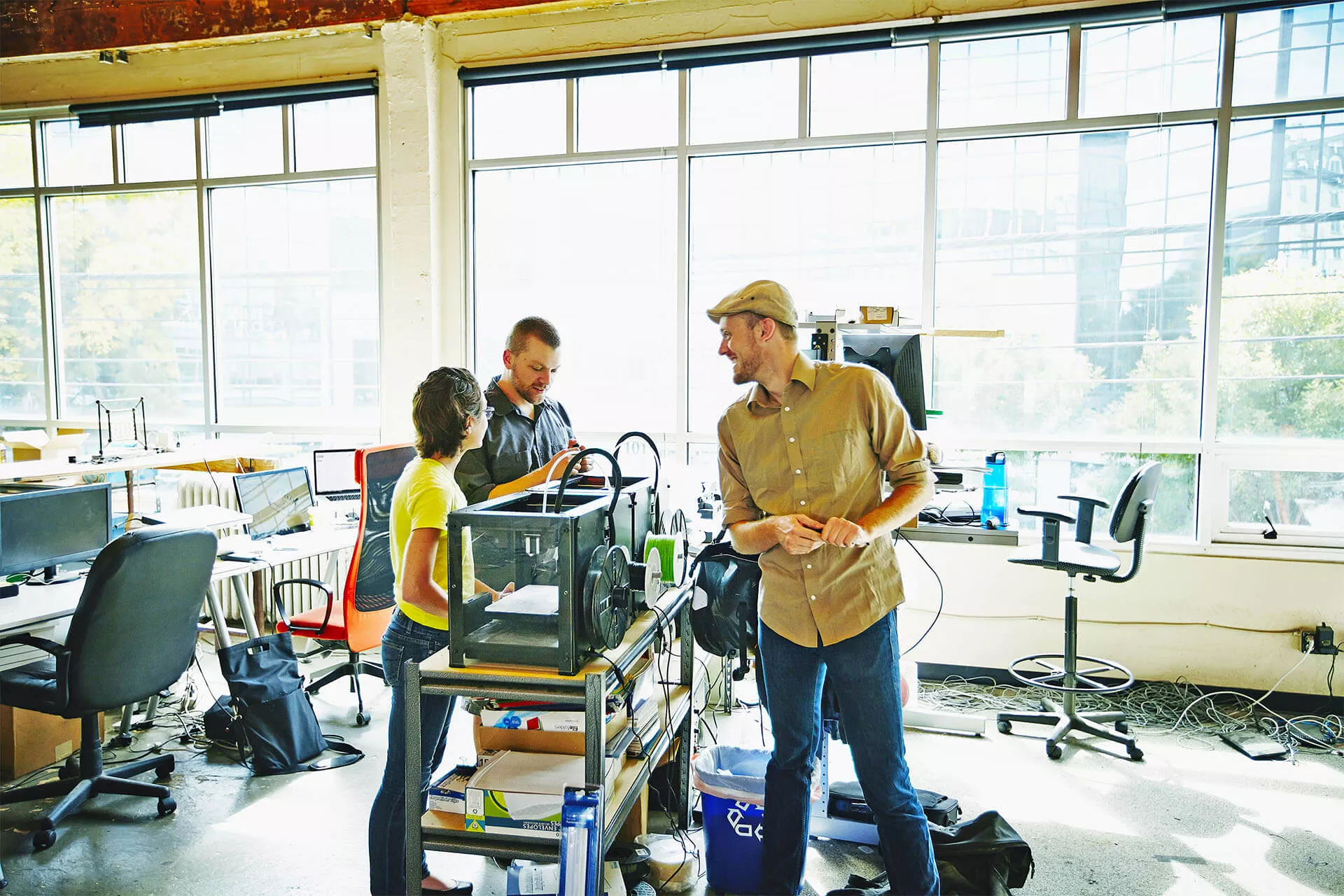
DIY, manufacturing of the future?
FabLabs (Fabrication Laboratories) or “maker workshops” are popping up everywhere, allowing anyone to prototype, test and manufacture products and ideas using sophisticated yet accessible technologies. Bringing DIY1 up to date, this dynamic, focussed on innovation and creativity, is opening up the exploration of more sustainable, sensible and autonomous models. What if it is marking the start of a new era for our economy, our industries and our way of life?
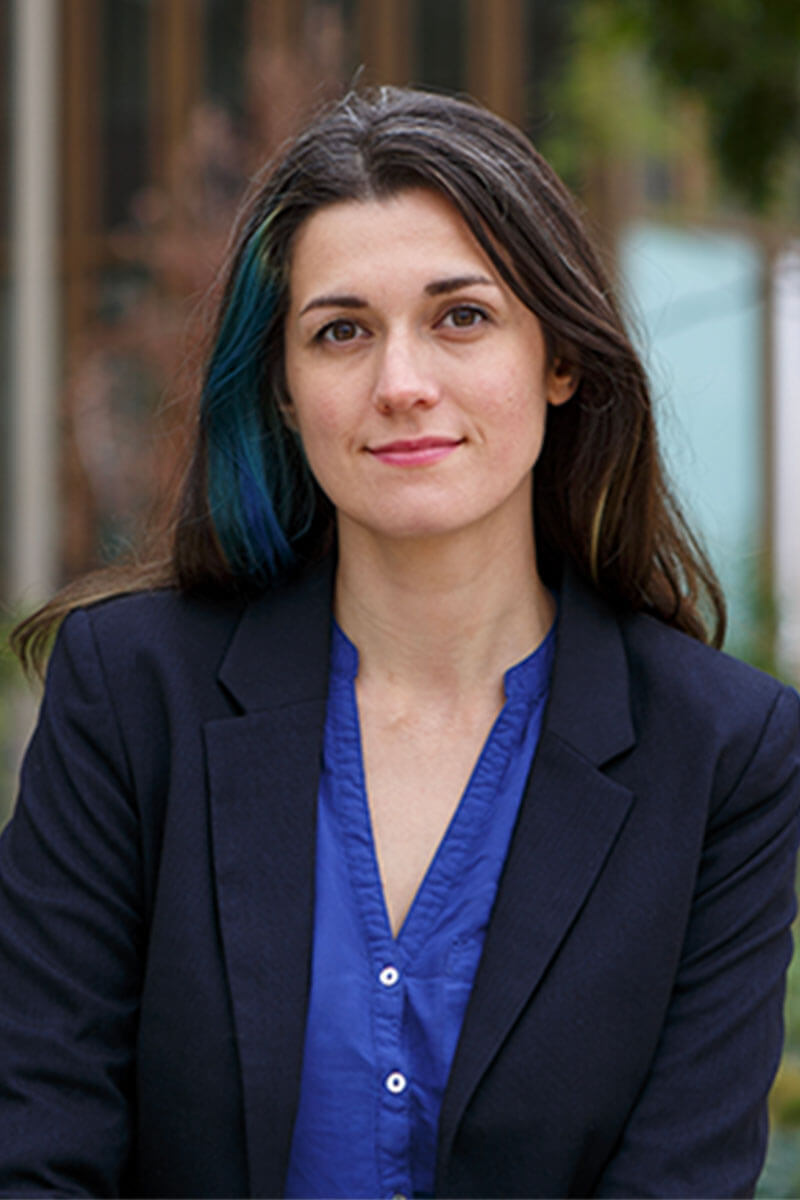
Mathilde Berchon
Founder of FuturFab, a consulting laboratory for Do-It-Yourself entrepreneurs, communications expert for the ANCT’s 100 Local Manufactures incubation programme and author of several works on 3D printing and its role in the industry of the future.
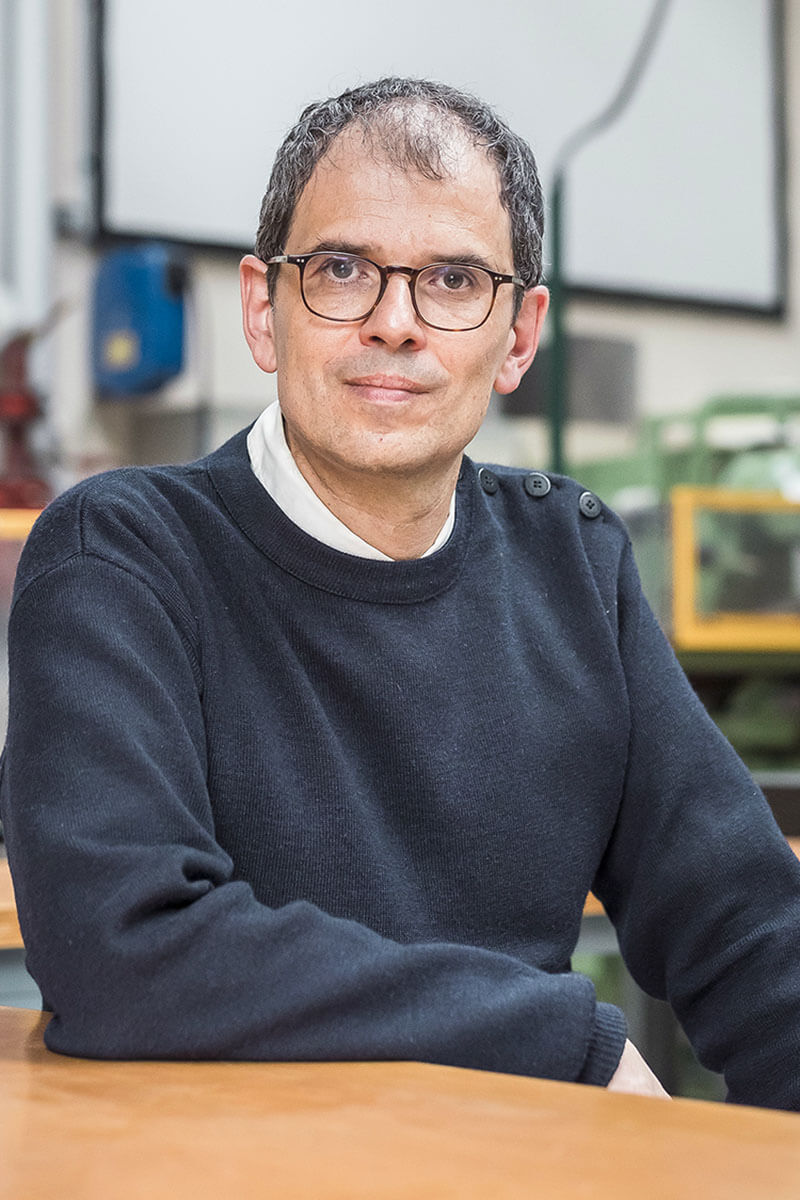
Jean-Marc Benguigui
Teacher of engineering, responsible for the Ecological Transition Engineering and Low-tech Engineering options at Nantes Central Engineering School. His teaching focuses on the low-tech approach, the circular economy, eco-design, carbon accounting and life cycle analysis.
Long hidden away, the maker2 movement is becoming more and more important. How do we explain this growth?
Mathilde Berchon: This movement, and the production spaces associated with them — FabLab, maker-spaces , local factories — emerged in the United States at the beginning of the 2000s, and a few years after that in France. They are shared, collaborative spaces open to all, where everyone can access machines and tools free of charge to design, experiment, and create and manufacture prototypes or objects. What characterises the functioning of these spaces is the philosophy of collaboration and open source3, which allows us to share manufacturing processes, tools and know-how. Everything that is created and learned must be documented and shared. Information, such as material specifications, is made available to the public, thus promoting creation and innovation within a community. In France, these maker ‘third-party spaces’ began to develop from 2009 and it was the pandemic which particularly highlighted their potential. During the first lockdown, when global supply chains were failing, regional FabLabs, cooperatives and individuals found ways to work together to manufacture and distribute visors, masks and medical equipment using 3D printers. This unprecedented mobilisation revealed that decentralised manufacturing could provide an alternative to current production and supply systems. This period served as a springboard for French FabLabs, allowing them to experiment with DIY on a large scale.
Jean-Marc Benguigui: The rise of FabLabs can also be explained by technological advances, notably the Internet and open source, which allow DIYers to easily make and repair objects, and to share their knowledge with a community. The return of doing it yourself also responds to a quest for meaning and a questioning of our modes of consumption and production, at a time of overconsumption and increasing climate issues. We have become essentially a service economy, transferring our production capacities to the countries of the South and the East, leaving us vulnerable. Current crises highlight the importance of being resilient and regaining control over production.
MB: Basically, I think that the makers movement is driven by the desire of individuals to move from passive conservation mode to active conservation, regaining control of their levels of consumption.
1. “ Do-It -Yourself “.
2. “Makers”, those who make.
3. Originally, the principle of open source refers to the design of software with open source code that is not based on proprietary principles.
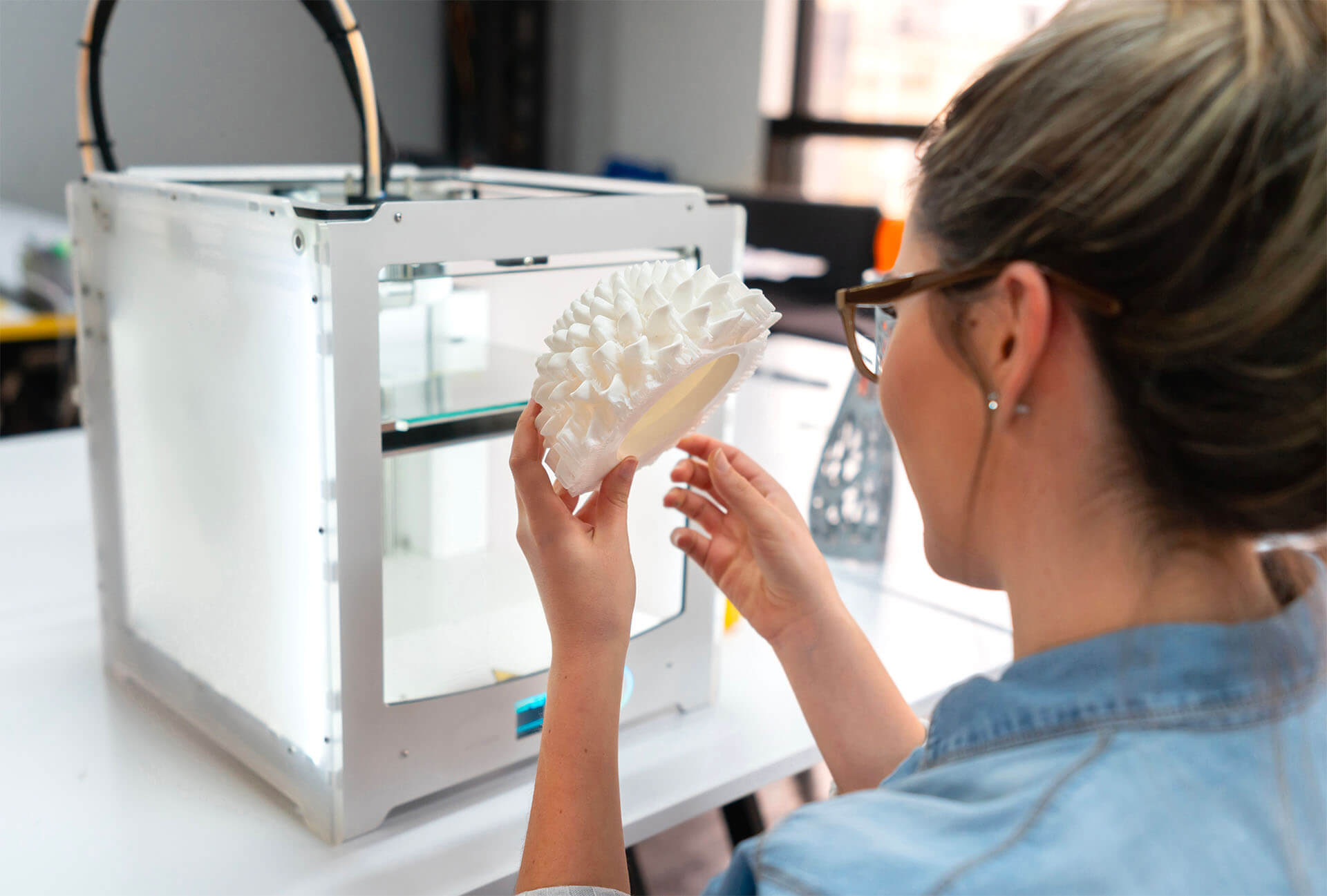
...Today, this movement is international. What does this represent in France?
MB: Initially, it was based on a network of fragmented locations, which existed thanks to the energy of a few volunteers. Today, it is a structured and durable movement, which benefits from the support of public authorities, with national associations, such as France Tiers-Lieux, RFFLabs, and the National Association of Third Places. In France, the movement is lively with major events like OctoberMake, the annual meeting of RFFLabs, not forgetting FabLabs, Espaces du Faire and the French makers movement... Today, there are 3,500 third-party locations, which have generated 882 million euros in turnover. 28% are FabLabs and 16% are shared craft workshops, i.e. 1,500 locations dedicated to the “maker” dynamic. This ranges from very small locations to large spaces of 1,500 m2. The profiles of makers are very varied, with DIY fans, craftsmen, students, associations, engineers, entrepreneurs and businesses.
What technologies are used in FabLabs?
MB: The FabLabs are almost all equipped with computer-controlled 3D printers to model, prototype or repair a product based on a plan. We also generally find very popular and easy-to-use laser cutters for cutting or engraving a material such as wood, metal, etc. Vinyl cutters are available for making stickers, plus digital embroiderers or even heat presses (imprinting images on textiles). More elaborate machines, such as the plastic injection press can collect plastic waste, crushing and transforming it into new objects (such as a kitchen worktop).
J-MB: There is a very strong link between FabLabs — spaces where you can do everything in a simple way — and “Low-Tech”, which is characterised as an approach allowing the production of objects or innovations that are useful, durable and accessible to all, in order, ultimately, to reduce the environmental footprint of the things we own. Two other criteria define Low-Tech: local and autonomous production, the user having to be able to repair an object on their own, without depending on the manufacturer, which is certainly rare these days!
In FabLabs and Low-Tech, we therefore find these same notions of accessibility, usefulness and autonomy. And I see a growing interest among young engineers for low-tech solutions. These students in particular want to build a more resilient and sober world. They understand that this Low-Tech approach goes beyond the circular economy and eco-design. They wonder about “digital sobriety”, even those who are passionate about computing.
In FabLabs and Low-tech, we find these same notions of accessibility, usefulness and autonomy.
A brief history of FabLabs
While the first magazines devoted to DIY date from the beginning of the 20th century in the United States, it was in the 1970s, with the punk movement, that it undoubtedly all began. FabLabs (Fabrication Laboratory) were born in the United States in the early 2000s under the tutelage of Neil Gershenfeld, professor at MIT in Boston (Massachusetts Institute of Technology). His idea? Allow everyone to experiment, learn and make manufacturing accessible to all, by equipping their classrooms with industrial or digital machines. His goal? Promote creativity, innovation and entrepreneurship by empowering students to design and manufacture their own objects. He opened a space dedicated to creation in the heart of MIT: it was the birth of the first FabLab. Today, FabLabs constitute a global network of collaborative manufacturing spaces, accessible to all and contribute to innovation, creation and knowledge sharing.
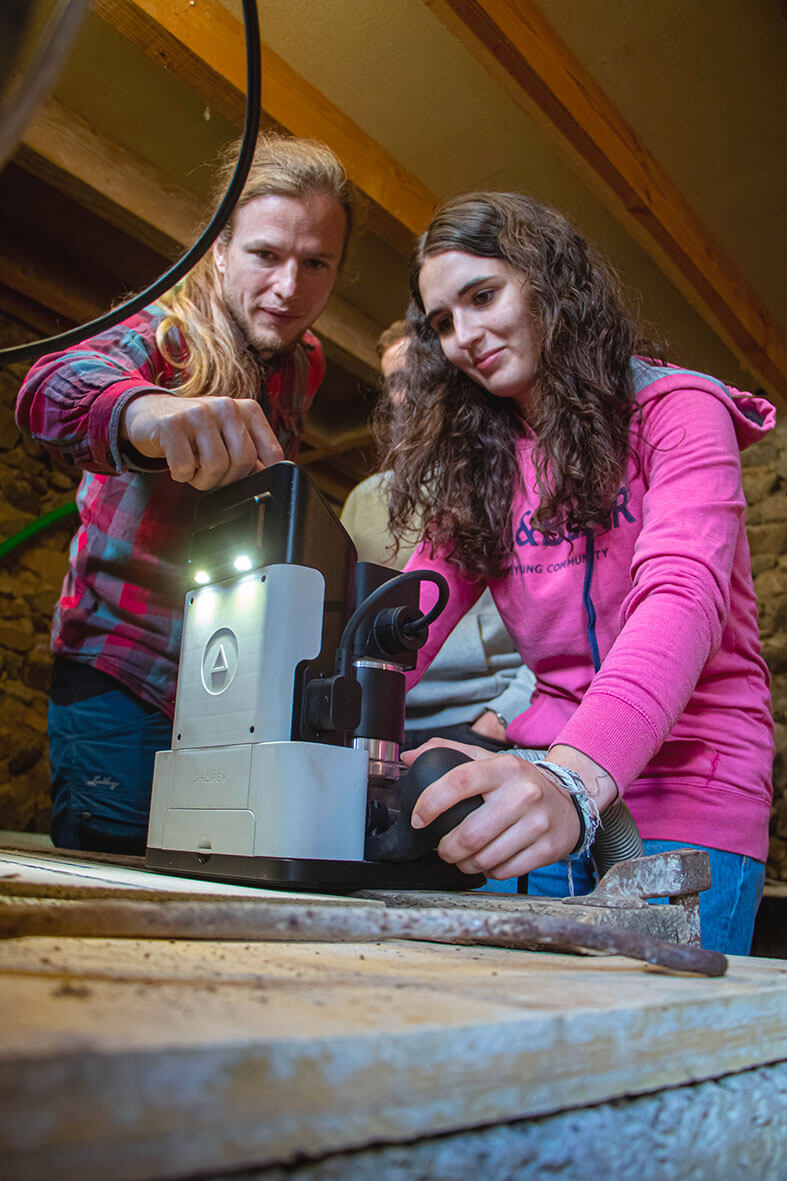
Are companies taking advantage of this phenomenon?
J-MB: With the various current crises (rising material prices, war in Ukraine), companies are becoming aware of how fragile they really are, with often a distinct lack of resilience. They turn towards FabLabs and Low-tech to gain the necessary agility. Overall, we see increasing interest from companies in low-tech engineering: they are questioning the usefulness of unbridled innovation and want to be as close as possible to the practical. Decathlon, for example, is thinking about product design by focusing on low-tech and eco-design. They have also launched a Low-Tech innovation competition. For their part, our students have a plethora of work-placement and job offers.
MB: Decathlon is indeed very active on the subject. They have a community of makers and opened several FabLabs to the public, thus allowing users (customers) to take part in the design of their products using 3D printers. This is why their products are ergonomic, user-centred and sold at the right price. Leroy Merlin is another company that was able to seize on this phenomenon in 2015, with the opening of its first “TechShop” in Ivry-sur-Seine, followed by another in Lille and then a third in 2018 on the Station F campus, in Paris. Their collaborative workshops are aimed at DIY enthusiasts, start-ups and universities who have at their disposal all the necessary equipment to create usable objects. We are seeing more and more companies relying on FabLabs to rethink their ways of designing a product. For example, we worked with a large group in the food industry to test packaging before launching it. Their teams came with packaging ideas, users and, in one day, we tested 25 ideas, selected the top 3 and chose the packaging, launching in record time only three months later.
What are the opportunities offered by maker spaces?
J-MB: This ‘return to the manual’ stimulates creation and creativity. Making or repairing an object allows you to develop a kind of practical intelligence, comparing theoretical ideas with actual reality, testing and prototyping the product and iterating for a final version. It also helps identify constraints and work out how to get around them. It’s much more than just DIY: starting from a concept, you have to know how to prototype, test, experiment... FabLabs are part of a sustainable economy where manufactured or repaired objects can become part of circular life cycles. They also help to encourage local production, which is a key issue as we increasingly highlight the question of reindustrialisation. This allows us to be more autonomous and less dependent on standardised production chains. Previously, the practice was taught in engineering schools and technical training courses. This is no longer the case and many engineers are moving into consulting. FabLabs are an interesting way to re-appropriate what manufacturing can be. We are also trying to launch a FabLab at the Nantes Central Engineering School.
MB: I think that entrepreneurs or large groups who want to innovate have every interest in having a local FabLab to prototype objects and test them.
Until recently, prototyping was an expensive and time-consuming process. Thanks to FabLabs, this essential step is now easier, faster and more economical. This also makes it easier to involve the user to better meet their expectations and to instil a dynamic of mutual aid and knowledge sharing. It should be noted that this corresponds to the early conceptualisation and prototyping phase, without consideration of the large-scale production phase.
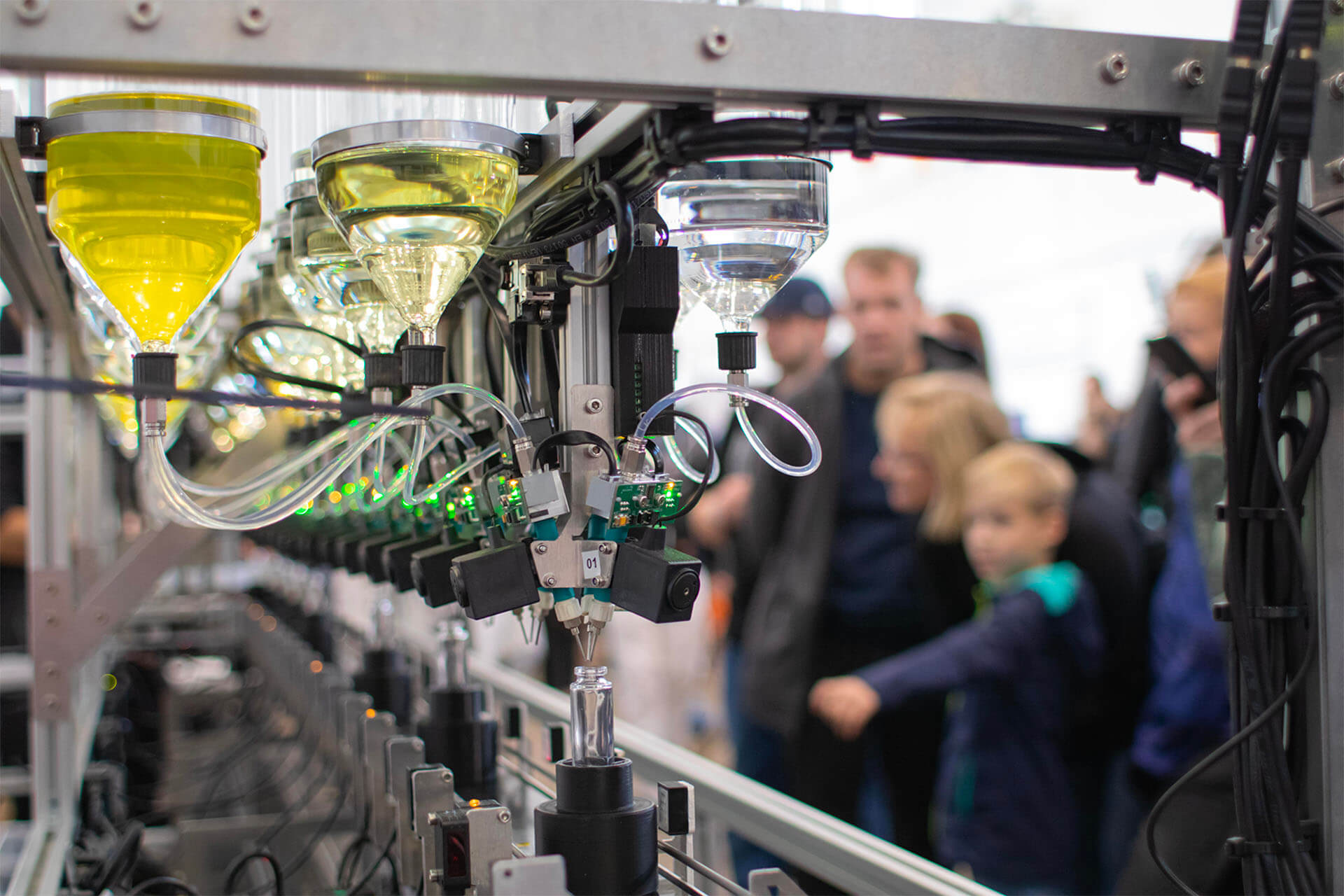
Can we imagine a future where DIY becomes a local manufacturing capacity, playing a central role in our economy and our lifestyles?
J-MB: DIY helps bring individuals back to doing and re-engages manufacturers in actual manufacturing rather than simply outsourcing. It could play a role in the increasingly necessary re-industrialisation of France. But judgement will need to be used to identify what should be repatriated and what should not. FabLabs and Low-Tech approaches have a real role to play when faced with the challenges of this new era of increased sobriety and preservation of resources. I think it is fundamental to the changing of our behaviour to adopt a more sober approach, to have a collective awareness of the need to preserve resources and to reconsider our needs. Low-Tech asks these questions while we are waiting for future technologies that will make it possible to cope with the runaway climate. In the past, many potentially useful technologies never even saw the light of day because, at the time, oil was a cheap and abundant resource.
The context is now different and this makes Low-Tech a viable solution while waiting for more advanced and environmentally friendly technologies to come on stream.
MB: We are still in the early stages of FabLab but this vision of regaining control of production is very much at the heart of what we do! If citizens develop the reflex to use FabLabs, regaining confidence in their ability to make, create, and to swap ideas and know-how, these spaces could become formidable engines of transformation! However, this requires a more personal approach and a change in our lifestyles. The transformative potential of FabLabs goes well beyond the design of objects, it also affects processes and working methods. Going to a FabLab means learning to do things together, breaking down the barriers between people and skills, and forming cross-functional teams. It’s a new way of thinking about manufacturing by focusing on a fundamentally decentralised approach.
At school, we learn theory first, then practice. In FabLabs, we learn by doing and it is by making mistakes that we go further. It’s difficult to understand until you have tried this experience yourself.
This is why I invite everyone to open the door of a FabLab!
Look further
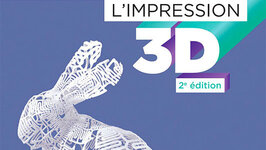
Books
3D printing
By Mathilde Berchon, with the collaboration of Bertier Luyt - Eyrolles, coll. Serial makers, 2014.
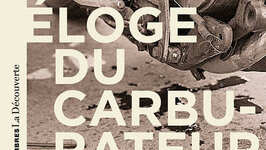
Shop Class as Soulcraft
By Matthew B. Crawford – La Découverte Poche, 2010.
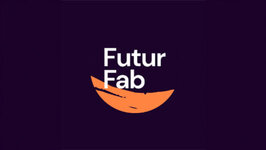
Websites
FuturFab - https://www.futurfab.fr
Kerlotec - https://kerlotec.com
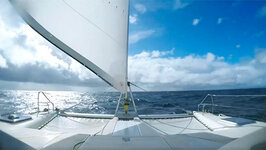
Documentary series
Nomade of the Seas, the stopovers of innovation
Series in 15 episodes by J. Offre, L. Sardi, S. Scorselo, V. Lefebvre. https://boutique.arte.tv/detail/Nomade_des_mers/
It is al ready tomorrow
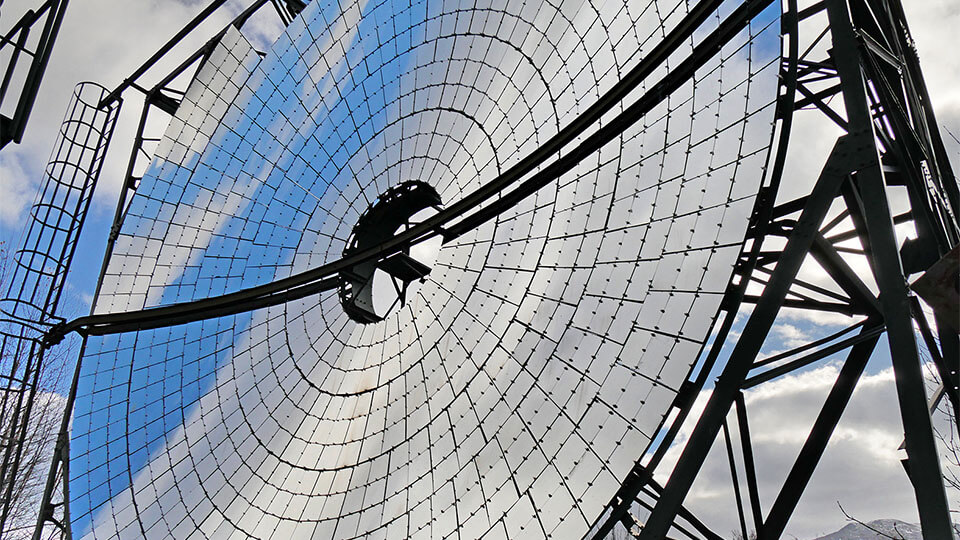
Solar rays to recycle steel
Swiss watch company Panatere will be the first in the world to use an industrial concentrating solar furnace to melt metal. This low-tech oven will be able, thanks to the concentration of rays from reflective mirrors, to reach a heat of 2,000°C and melt steel intended for the manufacture of components for watchmaking, the medical sector or aeronautics.
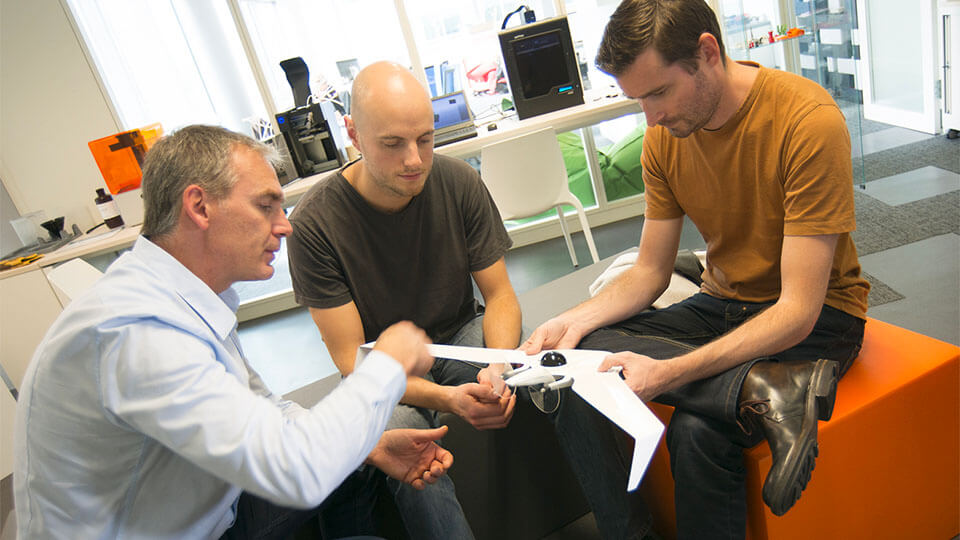
Innovations in health
In its 3DEXPERIENCE Lab, Dassault Systèmes makes its tools and skills available to collaborative innovation projects and start-ups. Aligned with the United Nations Development Goals, 3DEXPERIENCE enables many disruptive innovations to come to fruition. For example, Damae Medical (skin cancer detection device) or FEops (simulations for cardiac interventions).
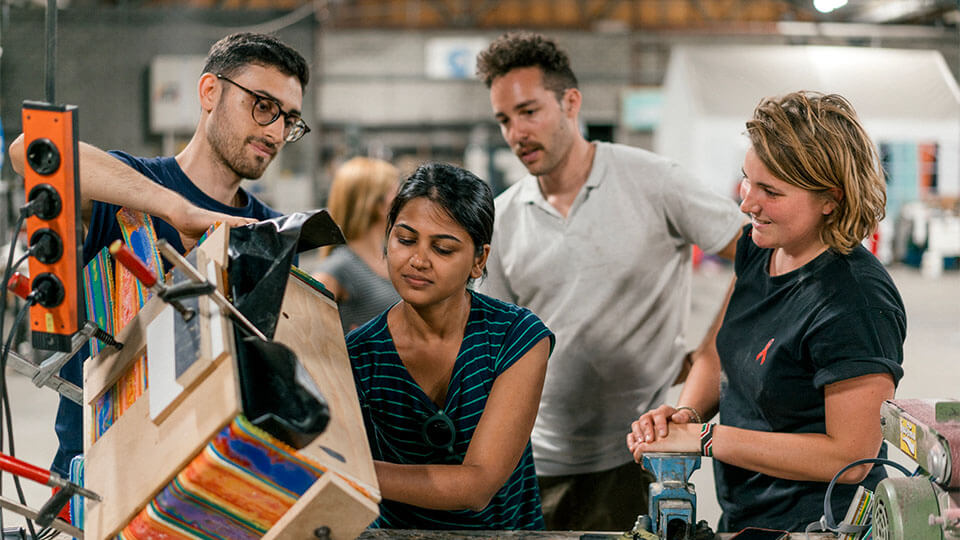
Towards self-sufficient cities
The first FabLab funded by the European Union in 2007, the Fab City of Barcelona contributes to the implementation of new models that will allow the Spanish city to “produce everything it consumes by 2054”. How? By relocating industries as close as possible to the city and modifying production practices for the benefit of a circular economy.
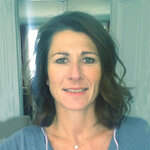
Text
Stephanie Livingstone- Wallace
A freelance designer-editor for more than 15 years, Stéphanie Livingstone- Wallace writes multiple communication media, with the energy transition, transport and logistics, education and finance and health as her preferred areas.